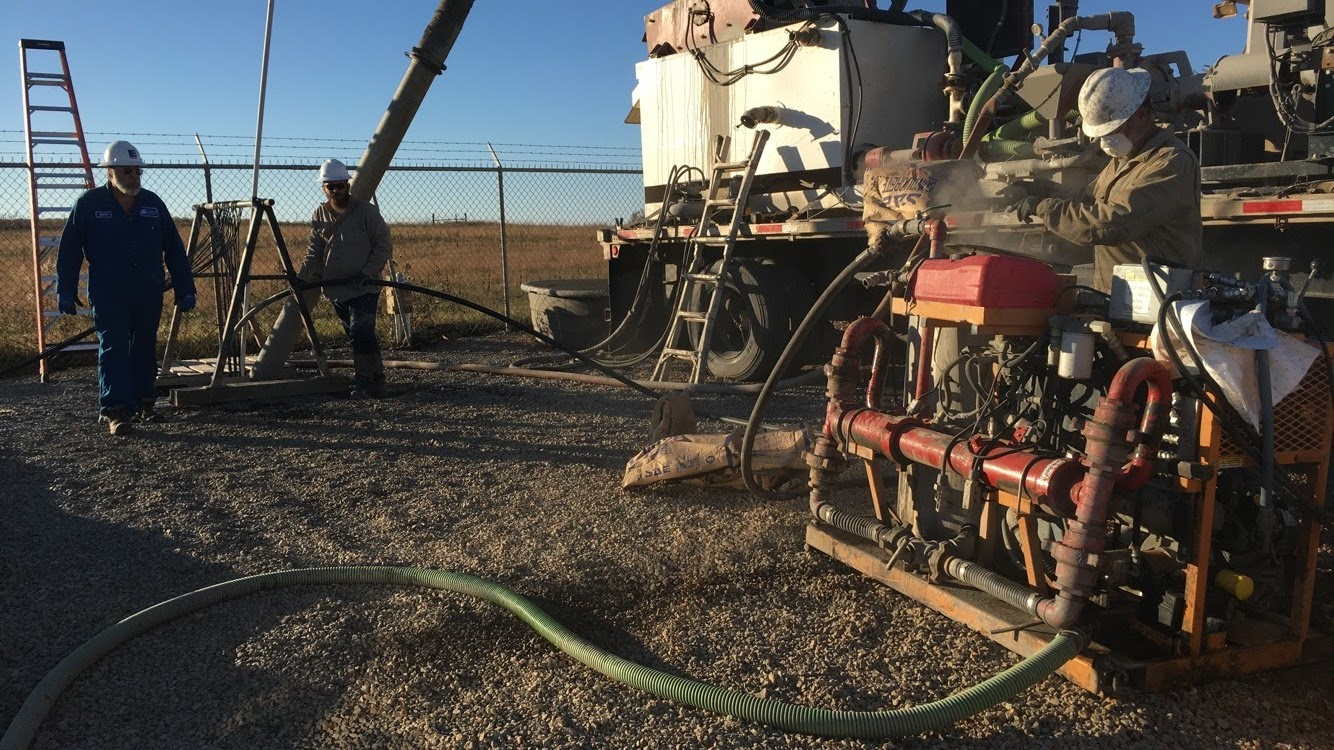
28 May Total Groundwater Protection
Disclaimer: Updated 06/15/2020
The purpose of this paper is to provide an opinion of the ability of the EnvirAnode® and Conducrete® Cathodic Protection System to protect groundwater resources by forming an impermeable seal within the installation borehole and effectively isolating different groundwater units. The following evaluation is based on review of technical and marketing literature, testing certifications, independent laboratory reports, and other data provided by SAE, Inc. in the context of groundwater protection. In addition, I personally witnessed installation of the EnvirAnode® CP system in a boring adjacent to a pipeline near Bloomington, Texas on April 2, 2014. In preparing this opinion, I have not performed any independent testing of the Conducrete® material and have relied on the veracity of information and data from independent laboratories provided by SAE, Inc. for this evaluation. Supporting documentation has been included as an appendix to this paper.
The EnvirAnode® cathodic protection (CP) system consists of a series of anodes embedded in an electrically conductive but geologically impermeable column made from Conducrete® backfill material. This system provides a number of benefits when compared to a shallow well CP system that is typically employed in areas of shallow groundwater including: reduced number of CP wells and sites, improved CP performance (i.e., better pipeline protection and reduced risk of corrosion failure), and extended lifespan of installed CP system. The EnvirAnode® CP system differs from traditional deep well CP systems in that the boring is backfilled with an impermeable cement (Conducrete®) whereas a traditional CP well is backfilled with porous carbonaceous material (e.g., coke breeze). In either system, the backfill reduces anode resistance to earth and extends the life of the anode. However, the backfill of a traditional CP well also provides a permeable pathway for produced gases to vent to the atmosphere. The permeable nature of the backfill limits the depth of the traditional CP well to the depth of the local water table or the base of the uppermost groundwater-bearing unit. This limitation often results in the need to install multiple shallow wells at a particular CP site instead of a single deep well. In addition, the shallow CP wells cause interference with other pipelines and are not as effective resulting in the need for additional well sites.
The EnvirAnode® CP system was evaluated with respect to three primary considerations for groundwater protection:
- Does the installation effectively isolate different groundwater units by forming an impermeable seal in the borehole?
- Is there any potential for groundwater contamination from the installed materials?
- Are there any concerns for cross-contamination during installation?
Does the installation effectively isolate different groundwater units by forming an impermeable seal in the borehole?
In order to securely seal a borehole, the column must be filled with a material of sufficiently low permeability that will maintain contact with all surfaces of the intersected formations along the wall of the boring. Grouts containing active solids, i.e., bentonite, offer the best opportunity to achieve borehole sealing. The most important factor is the sealing of void spaces once a drilling operation has taken place.
Conducrete® consists of a mixture of finely powdered Portland cement and fine carbon with no aggregates or sand. The reported permeability of the fully cured Conducrete® grout is 3.8×10-7 cm/sec, and shrinkage after 28 days is 0.015%. This permeability is within the range of commonly used grouts for sealing water wells (e.g., 3.7×10-7 cm/sec for bentonite-cement grout). During installation, dry Conducrete® powder is mixed with water to form a flowable cement paste which is pumped into the borehole through a tremie pipe. Because the Conducrete® is installed as a fluid and is pressurized by the displaced drilling mud in the borehole, the cement penetrates void spaces in the wall of the boring, thereby effectively sealing the boring and preventing water migration. Unlike in a water well wherein the grout must also effectively seal against the well casing material, Conducrete® forms a solid plug in the borehole and must only seal against the surrounding formation materials. Because of the clay content of geologic confining materials, it is expected that the Conducrete® would form an impermeable bond with the formation. The potential for separation of the Conducrete® from the formation caused by shrinkage during curing is minimal because of the extremely low shrinkage of Conducrete® and the elastic properties of geologic confining materials. Groundwater migration through the solid Conducrete® column or between the Conducrete® and the formation would be unlikely to occur.
A typical guideline1 for cement used in plugging of water wells calls for the use of 7 gallons of water per
94-pound sack of Portland or construction cement. This mix ratio produces a cement slurry with a density of 13.4 lbs/gallon. The recommended mix ratio for Conducrete® is 3.0 gallons of water per 55-pound sack of Conducrete®, producing a slurry with a density of 13.1 lbs/gallon. Based on this comparison, it appears that Conducrete® would be an acceptable material for plugging an abandoned water well in some areas.
Is there any potential for groundwater contamination from the installation materials?
According to the provided MSDS, Conducrete® is a mixture of Portland cement and powdered carbon and contains no aggregates. Portland cement is a common ingredient in borehole grouts, and powdered carbon presents no environmental concerns. SAE, Inc. recently received NSF/ANSI Standard 60: Drinking Water Treatment Chemicals – Health Effects certification2 for Conducrete® indicating that this product has been certified to be safe for use in drinking water wells.
SAE, Inc. provided a table of toxicity characteristic leaching procedure (TCLP) results for the Conducrete® material. TCLP is a soil sample extraction method for chemical analysis employed as an analytical method to simulate leaching through a landfill. Because the testing methodology is used to determine if a waste is characteristically hazardous, similar conditions are not expected in a typical groundwater environment, and the results would overestimate the amount of leaching that would occur.
The TCLP results are compared the to the Maximum Contaminant Level (MCL) established by the U.S. Environmental Protection Agency (USEPA) for each constituent in the table below. The MCL is the highest level of a contaminant that is allowed in drinking water. For those constituents detected in the leachate, none exceeded USEPA regulatory standards for drinking water. Several of the constituents were not detected, but the laboratory quantitation limit was greater than the MCL (see below for arsenic, lead, mercury and selenium). However, certification to NSF/ANSI Standard 60 ensures that Conducrete® meets USEPA drinking water requirements. Additionally, because of TCLP conditions, these constituents would not be expected to present a risk for migration in a typical groundwater environment.
Are there any concerns for cross-contamination during installation?
The time required for drilling the borehole for a deep CP well should be about one day, then four to six hours for placing anodes and pumping in the backfill with a tremie pipe. The borehole would only be open for a maximum of approximately 24 hours. This period of time is not sufficient to cause any significant environmental concern due to aquifer cross-contamination from an open hole during installation.
Observation of EnvirAnode® Installation
Installation of the EnvirAnode® CP system in a boring adjacent to a major pipeline system near Bloomington, Texas was observed on April 2, 2014. Personnel from SAE, Inc. were onsite to explain the manufacturing and installation process and to answer questions. SAE, Inc. also provided a design drawing for the CP well and samples of raw and fully cured Conducrete®.
The borehole was drilled on April 1, 2014 using a typical mud rotary drilling rig. For this CP system, the boring was drilled to a depth of 300 ft with the system of 12 anodes installed in the interval from 130 ft to 290 ft. The boring was backfilled with the Conducrete® material from 300 ft to 110 ft, bentonite from 110 ft to 4 ft, and native soil from 4 ft to the ground surface. The anodes are made of a carbon-resin composite surrounding a metal core and are shipped to the installation site with cables attached and pre-cut to the specified length at the factory. Each of the anodes was suspended in the borehole at the design depth, then the borehole was backfilled with Conducrete® using a tremie pipe. The Conducrete® was batch-mixed onsite before being pumped into the borehole. Following the observed installation of the anodes and placement of the Conducrete® grout, the borehole would be backfilled with bentonite chips to near the ground surface then the contractor would add the surface completion and connect the anode lead cables to the electrical panel. The system is not energized until a minimum of 30 days after completion to allow the Conducrete® material to fully cure.
Conclusions
Based on the evaluation discussed above and information provided by SAE, Inc., Conducrete®, when properly mixed and poured according to SAE’s specifications, forms a slurry with low permeability similar to bentonite-cement grout commonly used for sealing water wells. When fully cured, Conducrete® forms an impermeable column within the borehole that effectively seals the boring, isolating any groundwater-bearing units penetrated during drilling. Because of the low permeability and extremely low shrinkage of Conducrete®, it is expected that the Conducrete® would form an impermeable bond with the formation and groundwater migration through the solid Conducrete® column or between the Conducrete® and the formation would be unlikely to occur. It is my opinion that the EnvirAnode® CP system provides adequate protection of groundwater resources and does not pose any concerns for groundwater protection provided that the borehole is backfilled within 1 to 2 days of drilling and that the Conducrete® is properly prepared.
Download the white paper here.